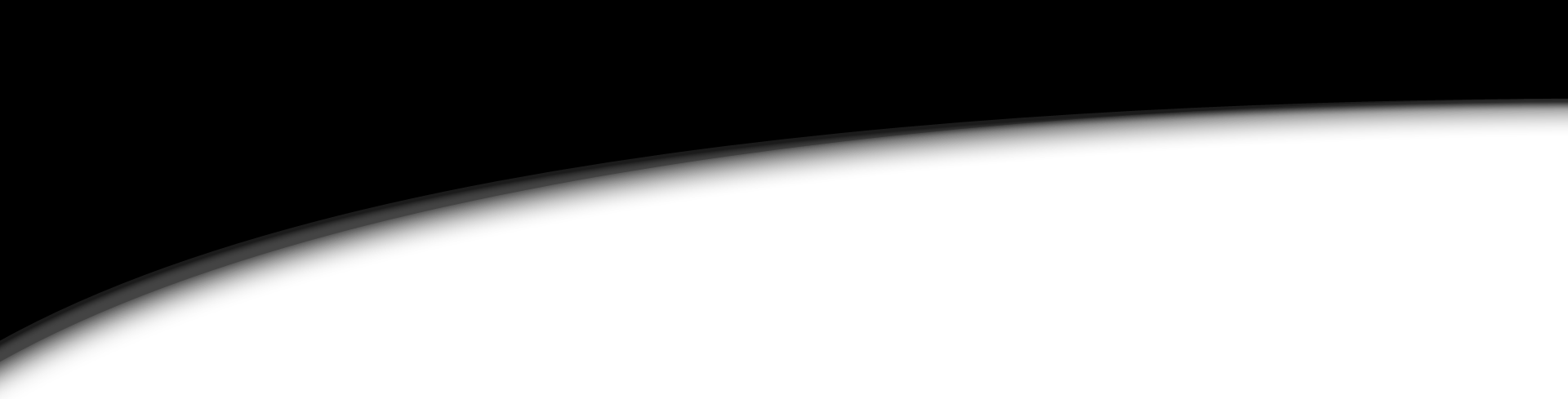

Equipment
Custom Plasma Foam Cutting Machine
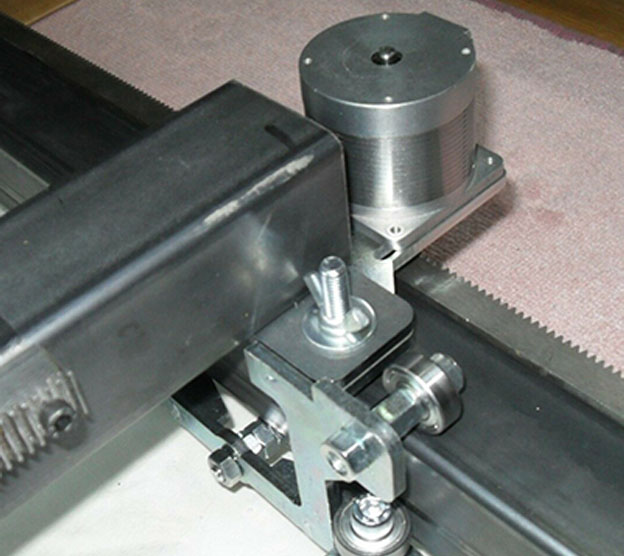
The goal of Samaan Coachworks is to fully customize classic BMWs to the extent that Hartge and Alpina did. That is potentially a gigantic cost if the production parts and prototypes are designed in house, but subcontracted out for manufacturing. Luckily, I have decades of experience both in industrial manufacturing and industrial design. More specifically, having a manufacturing job in the 21st Century means that I have inevitably have had to install or contend with computer controlled machinery. This is where the goals of Samaan Coachworks become feasible: CAD-CAM makes the creation of prototypes and production parts just a click of the mouse away.
CAD-CAM is very far along twenty years into the 21st Century. 3D printing services and 3D printing machines are relatively cheap. In fact, computer controlled routers and plasma cutters are within the purchasing power of small to medium sized shops, where in the 20th Century they were the high end equipment limited to the most specialized shops. A small shop can now print out parts out of plastic, and even metal to a limited extent. A small shop can even cut complex shapes out of metal and wood as plasma cutters have dropped dramatically in prices. I estimate that CNC technology in 2020 is about where desktop printing was in the 1980s or early 90s.
However, despite the fact that prices have dropped for ready-made CNC and 3D Printing machinery, the limitation is still size. Most of the affordable machines are desktop machines, capable of printing or cutting small parts. Clearly, that is a significant limitation if you are intent on making fully functioning parts for a full sized car, especially if you want to redesign the aerodynamics. In this case, size does matter! So, confronted with the limitation, I decided to make my own CNC plasma cutter. To tell you the truth, CNC controllers are simple compared to the computer controls of major industrial machinery, and the tables are nothing too difficult. In fact, it is relatively easy to make a “multi-process” machine. In my case, the machine in the above video will be able to swap out a plasma torch with a router, and convert from cutting metal to carving wood and foam.
Depicted in the video is the making of the table support and the refurbishing of an old water tank I found. Plasma cutters employ small pools of water to catch the sparks and smoldering metal the process produces. The making of the water tank was actually a significant hurdle, as bending metal that long is actually still something only larger and more sophisticated machine shops can do. Having found a tank of suitable size, I proceeded to design the rest of the table and systems around it.
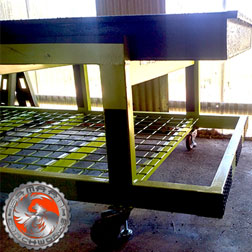
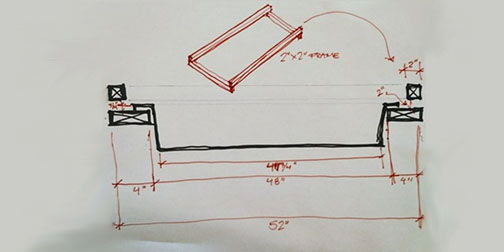
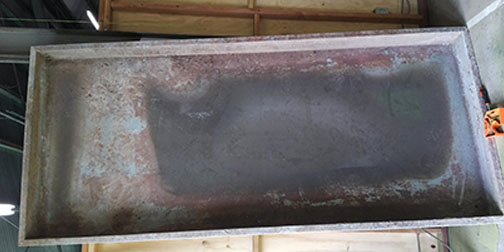
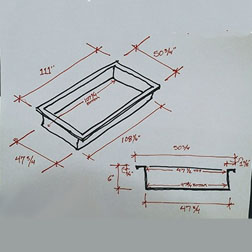
Samaan Coachworks – Custom Cylinder Head Workstation
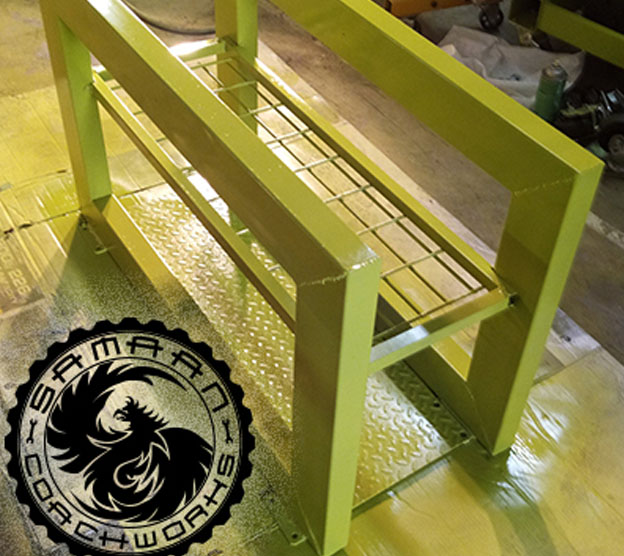
One of the most uncomfortable tasks in engine rebuilding is the disassembly and reassembly of the cylinder head. The cylinder heads of the 80s and 90s have components that are both delicate and under a lot of stress.The compresses springs are incredibly strong and stressed as the overhead camshaft is turned. You can’t simply lay the cylinder head on a table, because with each turn of the camshaft one of two of the valves pops beyond the bottom surface of the aluminum casting. The casting surfaces are themselves machined and must also be protected from marring or denting.
There are a lot of jigs available for American muscle cars available, but nothing really designed for a BMW M20 or M10 cylinder head. Therefore, I set out to design and build a station where the head can be held securely while forces are applied from all directions in the disassembling and reassembly of these heads.
This custom workstation has a small press for removing piston pins as well as spaces to for the storage of all the intricate and delicate parts that go in the BMW cylinder head assembly.
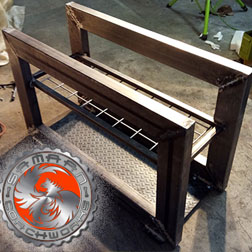
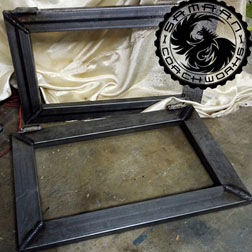
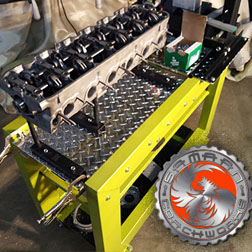
SAMAAN COACHWORKS – Custom Shop Workstations
Included here are pictures of three different projects to make “restomoding” easier. Samaan Coachworks started in a very small space with two cars. Anyone that has tried to fill a garage shop with professional tools knows exactly what a headache space management can be. However, there are certain tools that are indispensable for auto restoration and modification, namely metal shears, tube benders, sheet metal benders, and ways of moving the chassis around.
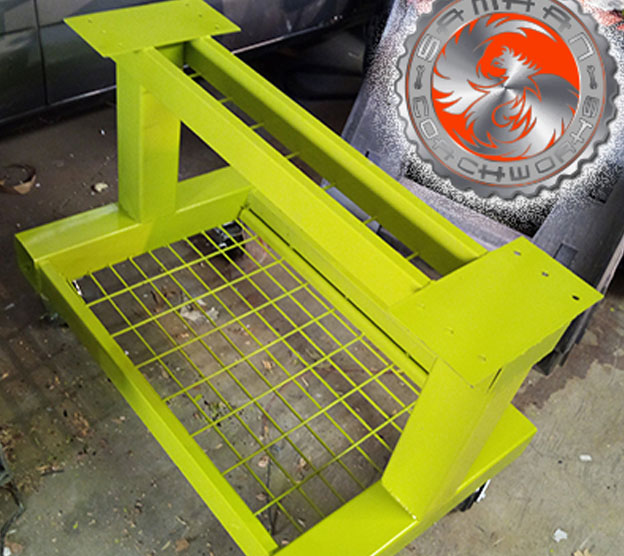
What is a Restomod? The restomod is a relatively recent phenomenon in the collector-car world. As a counterpoint to the “survivor” craze, these new cars mix old and new technology to create the best of both worlds, matching classic styling with modern comfort, performance and reliability.
The easiest, but one of the most important additions to a small garage shop is a cart for a dismantled chassis. There are wheel skates you can buy, but those have the drawbacks that they count on the actual wheels of the car being on, and the small wheels on these skates are hard to push around and get stopped up easily if they have to go over small screws or pieces that may be laying on the floor. Those are two big drawbacks, especially if you are doing a “frame off” rebuild, where the frame that the suspension and wheels bolt onto will be taken clear off the car. The solution is pretty easy. It involves four large casters, 16 lag bolts, washers, and nuts, and a couple of pieces of 2”x6” lumber. Take a couple of careful measurements of the car’s underside, make a few cuts of the wood, drill a few holes, bolt on the casters, and viola!!! You’ve got yourself a way to effortlessly support and move the bare bones chassis.
Metal shears and sheet metal bending tools are also a must for restoring decades old cars. It is almost impossible to find a rust-free chassis. There will be portions of sheet metal that have to be cut out and replaced with fresh sheet metal. This is how even a seemingly easy bend on a small piece of sheet metal will bring your build to a screeching halt. Doing precise cuts and bends is necessary, and the use of hand tools for this task is a sure way to make an otherwise fun job into a source of misery. Even the cheapest Chinese made shears and benders will make simple jobs as simple and grief free as they should be.
Last, but not least, any performance shop needs a way to bend metal tube. This is a necessary evil of improving the race-worthiness or street performance of an older chassis. There are countless uses for a tube bending station in a performance shop. Anything from a strut brace to a roll cage requires these tools. Samaan Coachworks is a street performance company, so we don’t need the sophistication other shops need in tube cutting and bending, but these tools are still necessary, and they need a sturdy base.
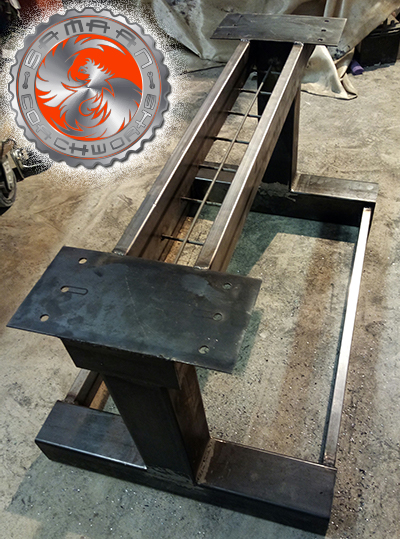
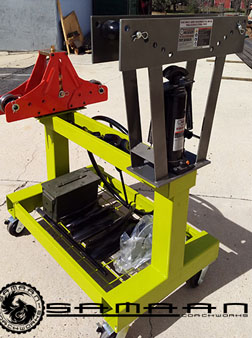
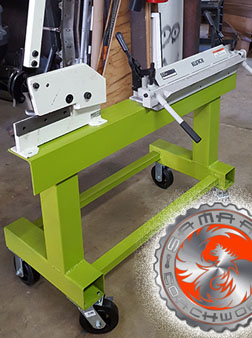
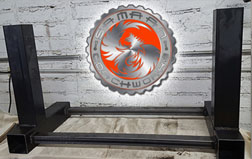
